Quality Assurance Specialist
The Blood Connection
Date: 2 weeks ago
City: North Charleston, SC
Contract type: Full time
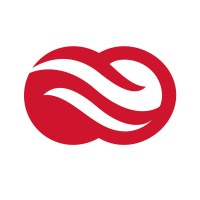
At The Blood Connection, every role plays a part in saving lives. Join our team and help make an impact in your community today!
Position Overview
The Quality Assurance Specialist provides support in the developing, coordinating, implementing, and evaluating quality assurance programs.
Essential Functions
Regulatory Issues:
The physical demands described here are representative of those that must be met to successfully perform the essential functions of this job. Reasonable accommodations may be made to enable individuals with disabilities to perform the essential functions.
Position Overview
The Quality Assurance Specialist provides support in the developing, coordinating, implementing, and evaluating quality assurance programs.
Essential Functions
Regulatory Issues:
- Assists Vice President, Quality Systems, with preparing an annual report to the Food and Drug Administration regarding minor changes that have occurred at The Blood Connection and its fixed sites
- Assists Vice President, Quality Systems, with submitting Prior Approval Supplement (PAS) which is required for a major change with a substantial potential for causing an adverse effect on identity, strength, quality, purity, and potency of a product collected, prepared or tested at The Blood Connection and its fixed sites
- Assists Vice President, Quality Systems, with submitting Changes Being Effected in 30 Days supplement (CBE30), which is required for a moderate change with a moderate potential to have an adverse effect on a product collected, prepared or tested at The Blood Connection and its fixed sites
- Assists Vice President, Quality Systems, and the respective departments at The Blood Connection with the preparation of the submission of paperwork and components (if applicable) to the Food and Drug Administration for licensing of components
- Assists Vice President, Quality Systems, with insuring appropriate notifications and compliance to other licensing and accrediting agencies (out-of-state licensing requirements, pharmacy, CLIA, AABB, FACT and DHEC)
- Reviews the evaluation and assessment of donor eligibility for donor reentry
- Appropriately notifies donors of eligibility status after evaluation of donor reentry
- Assists with handling donor eligibility status inquiries
- Modifies donor/donation records as requested in accordance to AABB, FDA, any other entity, and TBC SOPs
- Aware of factors that indicate the need for training or retraining and communicating closely with the operational department on the needs
- Prepares training materials to be used for insuring personnel (new hire and existing) know and understand current good manufacturing practices and key quality center-wide policies and processes
- Performs competency evaluation for technical operational job codes
- Notifies appropriate department directors/managers or designees when a failure is discovered during competency evaluation
- Reviews the performance of validation plans and ensures adequate performance of processes and/or equipment
- Assists the company in the development and performance (if applicable) of validation protocols for critical processes
- Reviews donor screening process (DRF) for accuracy and completeness
- Makes appropriate modifications to donor’s donation record
- Initiates the appropriate hold for blood products not suitable for release and approves the release of blood products suitable for release that have been placed on hold
- Ensures the Quality System pre-labeling qualification checks have been completed prior to the transfer of laboratory results to the manufacturing computer system
- Assists in the running and reviewing of duplicate donor report for possible duplicate donors in the blood banking database
- Appropriately merges donor records in accordance with The Blood Connection’s Standard Operating Procedures
- Runs computer hold reports and reviews units placed on hold by the system (LifeTec)
- Registers donor screening and phlebotomy information when information has been captured manually and ensures electronic donor record information is complete
- Reviews and evaluates investigations and corrections of manufacturing errors and accidents (occurrences)
- Determines the severity level of occurrences according to current TBC Occurrence Management policies and procedures
- Ensures the immediate actions performed for occurrences are sufficient and appropriately documented
- Appropriately performs and documents the recall/withdrawal of components involved in a manufacturing error or accident
- Determines if root cause analysis is indicated for a manufacturing error or accident and appropriately routes the occurrence to the responsible department for the root cause analysis
- Ensures root cause analysis performed for a manufacturing error or accident is appropriately documented and accurate
- Notifies appropriate regulatory agencies of reportable occurrences
- Maintains reportable and non-reportable occurrences
- Monitors occurrences deemed to require monitoring
- Prepares occurrence tracking and trending reports
- Ensures appropriate follow-up actions (corrective and preventive) to occurrence reports are implemented and are effective
- Investigates and evaluates suspected post transfusion transmitted disease reports and other adverse reaction notifications
- Performs lookback notifications when required
- Performs the market withdrawal of components collected from a donor with a positive infectious disease test upon subsequent donation or of components that are deemed unsuitable whether from post donation information or manufacturing error
- Files donor registration forms
- Initiates the appropriate notifications if the integrity of the donor registration form has been compromised
- Assists in the transition of regulatory paper documents to electronic documents
- Assists in the compiling of records for external assessments
- Assists in the shredding of documents and maintenance of the documentation of the shredding
- Develops and maintains quality assessment surveys for the assessments of the quality systems
- Documents assessments on the appropriate quality assessment survey
- Documents non-conformances discovered during the assessment according to current TBC policies and procedures
- Ensures non-conformances are appropriately routed to the responsible department for investigation
- Ensures immediate and corrective actions are received for non-conformances deemed requiring a corrective action plan
- Reviews and evaluates immediate and long-term corrective actions documented on the Corrective Action Plan for appropriateness and acceptability
- Determines the effectiveness checks required to ensure the corrective actions documented on a Corrective Action Plan are effective
- Performs the effectiveness checks for corrective actions to non-conformances discovered during an assessment
- Documents the effectiveness check results and determines if corrective action is effective or additional corrective action measures are necessary
- Prepares the Corrective Action Plan with supporting documentation of the effectiveness check for the Vice President, Quality Systems, and Medical Director
- Maintains assessment surveys and associated documents
- Provides tracking and trending reports
- Assists in the defining of critical supplies
- Qualifies critical incoming supplies according to written specifications; some critical supplies will require the qualification to be performed by the department, thus, notification of the supply is done, and a review of the qualification is reviewed, filed and logged
- Properly handles critical supplies that do not meet written specifications
- Documents the qualification process and appropriately labels critical supplies available for use
- Assists maintaining change management activities for Quality Systems departmental and organizational operational projects
- Participates in change management activities providing regulatory and compliance guidance
- Actively participates in process improvements to improve the organization and its quality goals
- Assists in hosting external assessors evaluating TBC’s quality systems
- Assists in ensuring the integrity of the donor registration forms is not compromised during the period of time in which the QS Unit is performing their pre-labeling qualification checks and routes the forms to the appropriate person/place for filing
- Provides open communication with the Vice President, Quality Systems, Manager, Quality Operations, and the other members of the Quality Systems department
- Other duties as assigned or required
- BS Degree in Biological Science or equivalent and two years’ experience in a regulated environment; or Associates Degree or equivalent and four years’ experience in a regulated environment; or High School Diploma with six years’ experience in a regulated environment
- Strong understanding of good manufacturing practices
- At least one year of experience in a regulated environment
- Strong knowledge of Microsoft Access and Excel
- Ability to communicate effectively, tactfully, and courteously to patrons, donors, sponsors, and co-workers
- Ability to organize and prioritize workload and meet deadlines
- Ability to work with all levels and in a diverse work environment
- Ability to establish and maintain effective working relationships with staff, management, and peers
The physical demands described here are representative of those that must be met to successfully perform the essential functions of this job. Reasonable accommodations may be made to enable individuals with disabilities to perform the essential functions.
- Lifting up to 25 pounds
- Sitting, standing, or walking for an extended period
- Bending and twisting
How to apply
To apply for this job you need to authorize on our website. If you don't have an account yet, please register.
Post a resume