Production Manager
ATC Automation
Date: 1 day ago
City: Simi Valley, CA
Contract type: Full time
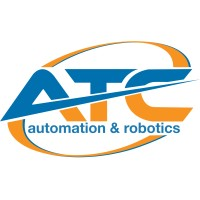
The Production Manager will be responsible for managing, leading, and developing the production team at ATC Simi Valley. This team consists of a variety of skill sets including mechanical assembly, electrical assembly, machine debug, and fabrication. This role is responsible for the build, debug and installation of various machinery and tooling projects. These may vary from small R&D tasks to large-scale production equipment. The Production Manager will work with other members of the leadership team, project management, and their team to deliver integrated and functional solutions to our customers.
How You Will Make a Difference:
ATC Automation and Robotics is committed to creating a diverse environment and is proud to be an equal opportunity employer. All qualified applicants will receive consideration for employment without regard to race, religion, color, national origin, sex, disability, age, veteran status, and other protected status as required by applicable law.
ATC Automation and Robotics is the Automation segment of TASI Group. The TASI Group of Companies is comprised of four technologically advanced Strategic Business Segments commonly linked by a disciplined focus on Product Integrity, Package Integrity, Automation and Flow. Each TASI company delivers world-class products and services, focusing on our global customer needs in diverse market segments. TASI has served several thousand global customers over the years and enjoys a very high rate of repeat customers, many of which are Blue Chip Global Companies. Major Markets include: Automotive, Medical Devices, Life Science, Pharmaceutical, Packaging, Oil & Gas, Food & Beverage, Consumer Goods and General Industrial Equipment.
How You Will Make a Difference:
- Lead and manage a team of mechanical, electrical, and Automation technicians to deliver integrated automated solutions
- Lead and manage a team of machinists to fabricate quality parts within budget and schedule.
- Manage and plan resources, manage contractors, oversee hiring and onboarding of new employees
- Manage the installation of equipment at customer facilities and ensuring a positive experience for the customer
- Ensure a safe work environment
- Develop and grow the Production Team for future needs including the mentoring and training of existing team members
- Ensure general efficiency and productiveness in all production activities and continuously improving
- Proactively coordinate with Project Managers on budget, schedule, and roadblocks.
- Proactively coordinate with Engineers on ECOs, NCRs, or other technical roadblocks.
- Develop and enforce processes, procedures, and documentation for production activities, including training and safety.
- Demonstrated talent building and debugging automated equipment or equivalent
- Demonstrated ability to lead, mentor, and manage teams.
- Demonstrated experience with performance management
- Experience creating, monitoring, and responding to relevant production metrics.
- Demonstrated talent and track record in automation and machine design
- Excellent leadership skills
- Excellent problem-solving skills
- Excellent written and verbal communication skills
- Demonstrated excellence in cross team collaboration
- Experience in troubleshooting automated equipment
- Broad knowledge of materials and fabrication processes (machining, welding, etc.)
- Ability to read and critique assembly and engineering drawings
- 5+ years in an industrial automation and/or machine building environment
- OSHA 30 Certified
- Bachelor's Degree, preferably in engineering or manufacturing
- Experience in tooling design and / or machine design
- Hands on debug, machining, and assembly experience
- Experience interfacing with customers
- Experience with implementing 5S initiatives
- Experience with pneumatic components and systems
- 7+ years an industrial automation and/or machine building environment
- Understanding of GD&T, Y14.5M-2009
- Familiarity with controls and software concepts
- Stand, walk, push, pull, reach overhead, and bend to floor.
- Exert 20 to 50 pounds of force occasionally.·
- Exert 10 to 25 pounds of force frequently.
- Exert up to 10 pounds of force constantly to move objects.
- VISUAL ACUITY: Near acuity with or without accommodation.·
- HEARING Ability: Ability to monitor machine sounds to identify and diagnose.
ATC Automation and Robotics is committed to creating a diverse environment and is proud to be an equal opportunity employer. All qualified applicants will receive consideration for employment without regard to race, religion, color, national origin, sex, disability, age, veteran status, and other protected status as required by applicable law.
ATC Automation and Robotics is the Automation segment of TASI Group. The TASI Group of Companies is comprised of four technologically advanced Strategic Business Segments commonly linked by a disciplined focus on Product Integrity, Package Integrity, Automation and Flow. Each TASI company delivers world-class products and services, focusing on our global customer needs in diverse market segments. TASI has served several thousand global customers over the years and enjoys a very high rate of repeat customers, many of which are Blue Chip Global Companies. Major Markets include: Automotive, Medical Devices, Life Science, Pharmaceutical, Packaging, Oil & Gas, Food & Beverage, Consumer Goods and General Industrial Equipment.
How to apply
To apply for this job you need to authorize on our website. If you don't have an account yet, please register.
Post a resume