Manufacturing Equipment Performance Specialist
Formerly Summit Biosciences Inc. | KDD
Date: 9 hours ago
City: Lexington, KY
Contract type: Full time
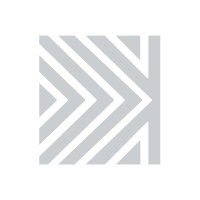
Our Work Matters
At Kindeva we make products that save lives, ensuring better health and well-being for patients around the world.
As a Manufacturing Equipment Performance Specialist, you will play a key role in maximizing equipment efficiency, minimizing downtime, and ensuring regulatory compliance within our manufacturing environment. Your hands-on support and analytical insight will help drive continuous improvement initiatives and support the integrity of our production systems. By troubleshooting issues, analyzing performance data, and supporting qualification activities, you’ll directly contribute to the quality, reliability, and success of our pharmaceutical operations. Your work will not only improve productivity and efficiency but also uphold the high standards needed to deliver life-saving treatments to patients worldwide.
Responsibilities:
Equipment Performance and Troubleshooting
Basic Qualifications:
California residents should review our Notice for California Employees and Applicants before applying.
Equal Opportunity Employer:
Kindeva Drug Delivery is an Equal Opportunity/Affirmative Action Employer and does not discriminate on the basis of race, color, religion, gender, age, national origin, disability, Protected Veteran status, sexual orientation, or any other characteristic protected by federal, state or local law.
At Kindeva we make products that save lives, ensuring better health and well-being for patients around the world.
As a Manufacturing Equipment Performance Specialist, you will play a key role in maximizing equipment efficiency, minimizing downtime, and ensuring regulatory compliance within our manufacturing environment. Your hands-on support and analytical insight will help drive continuous improvement initiatives and support the integrity of our production systems. By troubleshooting issues, analyzing performance data, and supporting qualification activities, you’ll directly contribute to the quality, reliability, and success of our pharmaceutical operations. Your work will not only improve productivity and efficiency but also uphold the high standards needed to deliver life-saving treatments to patients worldwide.
Responsibilities:
Equipment Performance and Troubleshooting
- Lead efforts to monitor and optimize the performance of manufacturing equipment and ensure compliance with CGMP standards
- Troubleshoot and resolve complex issues to minimize production downtime.
- Identify and implement opportunities for continuous improvement through upgrades, process modification, or alternative solutions. Lead in the development and implementation of procedural or automation improvement changes.
- Lead lean manufacturing initiatives, six sigma projects, and other process optimization efforts to improve productivity, quality, and cost efficiency.
- Assist with new product/equipment design reviews, process development and commercialization activities including training and development of manufacturing staff on operation and process.
- Serve as a technical point of contact for client and contract services
- Assist with manufacturing equipment-related deviations and root cause analysis as the equipment SME.
- Support the development and execution of Corrective and Preventive Actions (CAPA) and Change Controls to address root causes of equipment failures and performance issues.
- Support equipment Installation, Operation, Performance Qualification (IOPQ) activities
- Provide SME input on equipment qualification processes ensuring fit for commercial manufacturing use, compliance with FDA and other regulatory requirements.
- Other duties as assigned.
Basic Qualifications:
- Bachelor’s degree in engineering or related field and/or equivalent experience.
- 2-5 years of relevant experience in the pharmaceutical manufacturing industry with a focus on equipment and process improvement. Knowledge of GMP and regulatory requirements in the pharmaceutical industry.
- Proven track record of successfully implementing improvement initiatives in a pharmaceutical manufacturing environment.
- Strong analytical and problem-solving skills with the ability to use data to drive decision-making.
- Excellent communication and interpersonal skills, with the ability to influence and collaborate effectively across multiple departments.
- Ability to manage multiple projects and priorities in a fast-paced environment.
- Experience with automation, nasal or related drug delivery device manufacture and packaging.
- Lean manufacturing or six sigma certifications
- Proficiency in using Lean tools and software applications such as Smartsheet, Power BI, Power Apps, etc.
- Specific vison requirements include; close vision, distance vision, color vision, and the ability to adjust and focus in order to read/understand/execute documentation as required by the position
- Employee are required to follow all cGMP and safety procedures.
- The employee must wear all required safety equipment and perform assigned work in a safe manner.
- Employee must use proper lifting techniques and be conscious of hazards around him/her.
- Must follow all GMP and safety procedures within the department.
- The employee must occasionally lift and/or move up to 20 pounds.
California residents should review our Notice for California Employees and Applicants before applying.
Equal Opportunity Employer:
Kindeva Drug Delivery is an Equal Opportunity/Affirmative Action Employer and does not discriminate on the basis of race, color, religion, gender, age, national origin, disability, Protected Veteran status, sexual orientation, or any other characteristic protected by federal, state or local law.
How to apply
To apply for this job you need to authorize on our website. If you don't have an account yet, please register.
Post a resume