Quality Engineer
HOERBIGER
Date: 2 weeks ago
City: Waukegan, IL
Contract type: Full time
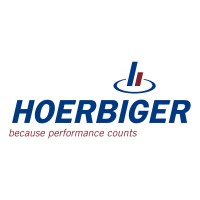
Your Mission
The Quality Engineer supports internal and external customers to mitigate problems and identify opportunities for improvement to ensure customer satisfaction, compliance and that Key Performance Indicators (KPIs) are met and/or exceeded.
How you will make a difference
The Quality Engineer supports internal and external customers to mitigate problems and identify opportunities for improvement to ensure customer satisfaction, compliance and that Key Performance Indicators (KPIs) are met and/or exceeded.
How you will make a difference
- Customer Support: Serve as point of contact for customer quality issues. Lead the investigation and resolution of customer complaints including root cause analysis and implementation of corrective/preventive actions. Manage customer communication and documentation (8Ds, SCARs, PPAPs, FAIRs). Work with production to determine causes of non-conformance. Participate in design reviews to ensure manufacturability of product.
- Material Compliance: Ensure materials comply with requirements such as RoHS, REACH, Proposition 65, conflict minerals). Manage material declarations, certificates of compliance and supplier material data. Respond to customer requests for compliance documentation. Work with Purchasing, Engineering and Supplier Quality to ensure upstream compliance in the supply chain.
- Internal Collaboration and Quality Systems: Communicate Customer expectations and complaints across production, engineering and supplier quality. Lead cross-functional teams in resolution of nonconforming products and systemic quality issues. Contribute to internal quality improvement initiatives. Track and report on customer quality metrics (PPM, on-time responses, NCR trends). Use QMS tools to manage issue resolution, maintain traceability and document compliance.
- Minimum 3 years’ experience in Quality Engineering or Customer Quality in a precision manufacturing setting with machined parts/devices.
- Bachelor’s degree in quality engineering, mechanical engineering, or similar major.
- Hands-on experience with root cause analysis, corrective action tools (e.g., 8D, FMEA, ISHIKAWA), and customer complaint resolution.
- Knowledge of material compliance regulations (RoHS, REACH, conflict minerals, etc.) and experience managing compliance data.
- Strong communication skills with the ability to interact effectively with customers and cross-functional teams; excellent written communication skills.
- Experience in using measuring equipment and reading blueprints in terms of GD&T.
- Proficiency in Microsoft Office, QMS platforms, and ERP systems.
- Green Belt certification or equivalent training in Lean Six Sigma preferred.
- Familiarity with industry standards (APQP, ISO 9001, IATF 16949, AS9100) preferred.
- Comprehensive Benefits: 401(k) plan with matching contributions, health insurance (medical, dental, vision), FSA and HSA options.
- Paid Time Off: Generous PTO and paid holidays for a healthy work-life balance.
- Professional Development: Educational assistance programs and opportunities for career growth.
- Supportive Environment: A stable, team-based culture that values collaboration and innovation.
- Inclusive Workplace: Join a company committed to equity, diversity, and inclusion, fostering a culture of belonging.
- Workplace Flexibility: Hybrid work schedule with remote work options after onboarding.
How to apply
To apply for this job you need to authorize on our website. If you don't have an account yet, please register.
Post a resume