Manufacturing Engineer
RIX Industries
Date: 3 weeks ago
City: Sparks, NV
Contract type: Full time
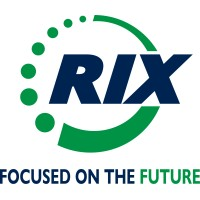
Job Type
Full-time
Description
RIX Industries manufactures a wide range of pneumatic energy storage and transfer system solutions, including reciprocating piston compressors and gas generators and liquefiers for industrial gasses and breathing air. RIX specializes in applying oil-free technology to high-pressure applications and other highly demanding environments. RIX has been in business since 1878 and has been proudly serving our US Armed Forces for over 120 years. With a solid industry reputation that is second to none, RIX is the established leader in American-made compressor engineering and manufacturing.
Position Summary
The Manufacturing Engineer is primarily responsible for promoting operational excellence in the RIX Value Stream including both internal and external processes. This position exercises proactive influence over day-to-day operations, seeking to promote maximum efficiency in manufacturing, assembly, and test workflows. The role will develop operational processes, and implement efficient capitalization, with the intent of minimizing cycle times and cost in general, while striving to prevent value stream failures. When failures do occur, this position will drive effective and efficient root cause corrective action. The Manufacturing Engineer is responsible for promoting the continuous improvement of RIX operations in general.
Responsibilities
Minimum Qualifications
This position is regularly exposed to the following conditions:
RIX Industries is committed to a continuing program of equal employment opportunity. All persons have equal employment opportunities with RIX Industries, regardless of their sex, race, color, age, religion, creed, sexual orientation, national origin, ancestry, physical or mental disability, medical condition (cancer or genetic characteristics), marital status, gender (including gender identity or gender expression), familial status, military or veteran status, genetic information, pregnancy, childbirth, breastfeeding, or related conditions (or any other group or category within the framework of the applicable discrimination laws and regulations).
Salary Description
$90,000 + DOE
Full-time
Description
RIX Industries manufactures a wide range of pneumatic energy storage and transfer system solutions, including reciprocating piston compressors and gas generators and liquefiers for industrial gasses and breathing air. RIX specializes in applying oil-free technology to high-pressure applications and other highly demanding environments. RIX has been in business since 1878 and has been proudly serving our US Armed Forces for over 120 years. With a solid industry reputation that is second to none, RIX is the established leader in American-made compressor engineering and manufacturing.
Position Summary
The Manufacturing Engineer is primarily responsible for promoting operational excellence in the RIX Value Stream including both internal and external processes. This position exercises proactive influence over day-to-day operations, seeking to promote maximum efficiency in manufacturing, assembly, and test workflows. The role will develop operational processes, and implement efficient capitalization, with the intent of minimizing cycle times and cost in general, while striving to prevent value stream failures. When failures do occur, this position will drive effective and efficient root cause corrective action. The Manufacturing Engineer is responsible for promoting the continuous improvement of RIX operations in general.
Responsibilities
- Interfaces with design engineering on new products, influencing the design toward a more producible, more easily assembled configuration.
- Develops, implements and improves methods, operation sequence and processes in the manufacture or assembly of parts, components, sub-assemblies and final assemblies.
- Makes recommendations for tooling and process requirements of new or existing product lines.
- Estimates manufacturing cost, determines time standards.
- Identifies and implements improvements to existing manufacturing processes, to improve safety, ergonomics, quality, and efficiency, and/or to reduce cost of goods sold.
- Establishes routings, methods, layouts, tools, costs, methods documentation, quality plans and labor standards for revisions to current operations and/or new parts or programs.
- Ensure manufacturing processes fully comply with all internal and external requirements, including but not limited to those stipulated by safety, regulatory, customer, and RIX Quality Plan requirements.
- Assist in evaluation of equipment to ensure compliance with safety and environmental regulations.
- Audit or monitor work in-progress to ensure conformance to set labor standards.
- Trouble shoot process and equipment issues and implement appropriate remedies.
- Coordinates with the QC team to ensure timely and accurate completion of activities related to NCRs, CARS, and other quality processes, including providing technical support and direction for rework activities.
- Coordinates and ensures completion of all activities related to implementation of Engineering Changes; ensures that BOMs and routings are up-to-date and are optimized to the design intent.
- Provide training to shop employees as necessary.
- Establish preventive maintenance schedules for equipment and tooling assigned to specified production.
- Facilitate and ensure effective communication between the various RIX functions and the manufacturing staff.
- Perform all other duties in the best interest of the company or as directed by the Manufacturing Engineering Manager.
- All Other Duties as Assigned
Minimum Qualifications
- Bachelor’s Degree in Industrial, Manufacturing, or Mechanical Engineering from an accredited college or university.
- A minimum of 3 years of relevant work experience in a manufacturing or industrial engineering role.
- Solid understanding of algebra and geometry, ability to apply advanced mathematical concepts such as exponents, logarithms, polynomial equations, and differential calculus.
- Understanding of mechanisms and how the parts interrelate in an assembly.
- Working knowledge of machine design and GD&T dimensioning.
- Working knowledge of detail part manufacturing, assembly processes and production workflow planning.
- Advanced understanding of Bill of Material (BOM) structuring and routings.
- Outstanding critical thinking, analytical and problem-solving skills, including a high-level of ingenuity and creativity.
- Excellent interpersonal, verbal, technical writing, and presentation skills.
- Outstanding leadership, planning, and time management skills.
- Basic computer skills with the ability to adapt to a variety of software applications (including: Autodesk-Inventor, Visio, Excel, and Project).
- Familiarity with and ability to perform basic cost accounting calculations such as ROI, NPV, and Cost of Goods
- Ability to communicate with others to exchange information both orally and in writing.
- Citizenship: U.S. Citizen or qualified U.S. Person in accordance with ALU 22CFR 120.15. May require the ability to obtain DOD security clearance.
- Experience implementing Lean manufacturing practices.
- Lean Six Sigma Certified
- Specific experience in the manufacture of complex machinery, and particularly promoting Design for Manufacture/Design for Assembly principles.
- Familiarity with basic business finance principles
- Working knowledge of DFM & DFA principles
- Formal training or experience implementing Lean principles and leading Kaizen events
- Basic LabVIEW or PLC programming skills
This position is regularly exposed to the following conditions:
- Manufacturing, warehouse and office environments
- While working near moving equipment, mechanical parts and lift trucks; must have the ability to follow safe operating procedures.
- May be exposed to loud noise, fumes and/or toxic chemicals.
- Ability to stoop, kneel, crouch, bend, stretch, reach, and lift.
- Ability to lift up to 50 pounds regularly.
- Ability to sit or stand for extended periods at a desk or table as well as machine tools or printers.
RIX Industries is committed to a continuing program of equal employment opportunity. All persons have equal employment opportunities with RIX Industries, regardless of their sex, race, color, age, religion, creed, sexual orientation, national origin, ancestry, physical or mental disability, medical condition (cancer or genetic characteristics), marital status, gender (including gender identity or gender expression), familial status, military or veteran status, genetic information, pregnancy, childbirth, breastfeeding, or related conditions (or any other group or category within the framework of the applicable discrimination laws and regulations).
Salary Description
$90,000 + DOE
How to apply
To apply for this job you need to authorize on our website. If you don't have an account yet, please register.
Post a resumeSimilar jobs
Production Process Engineer
American Battery Technology Company,
Sparks, NV
1 hour ago
OverviewAmerican Battery Technology Company (ABTC) is an industry-leading battery metal and critical materials technology development and commercialization company. Our Pilot Plant in Sparks, Nevada will be the first integrated implementation of our multi-step processing train for the full mechanical processing, physical separations, chemical extractions, and production of commercial-scale battery metals that will be resold back into the battery manufacturing supply...
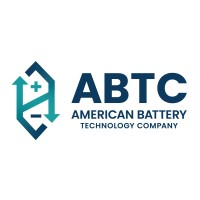
Construction Superintendent
Tesla,
Sparks, NV
23 hours ago
What To ExpectWe are seeking a highly experienced and results-driven General Superintendent to oversee and manage construction projects in and around an active manufacturing facility. This role is responsible for ensuring that all aspects of the project, including safety, scheduling, quality control, and cost management, are executed efficiently and in compliance with industry regulations. The General Superintendent will lead field...
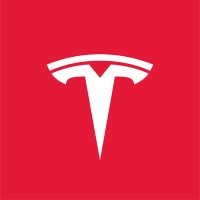
Northern Nevada Sales Manager
Vin Sauvage,
Sparks, NV
2 weeks ago
Vin Sauvage is family-owned, craft beverage wholesale company that has been servicing the state of Nevada for over 20 years. We are looking for a craft beverage and fine wine focused individual to oversee our Northern Nevada sales team.Our hope is for the Regional Manager to be an impactful sales and marketing professional, who will promote the full portfolio in...
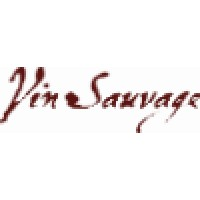